road.cc visited Canyon Bikes in Koblenz, a small city nestled on the banks of the River Rhine just a short drive from Cologne airport. We arrived on an unseasonably hot day to have a look around the assembly facility and offices of a brand that's growing fast in the UK.

This is where it all started. Founder Roman Arnold and his brother Franc used to buy bicycle parts from Italy and sell them at races around Germany. In 1985 they started a bike parts supply company, Radsport Arnold, and in 2001 took the big step to start manufacturing bicycles. Canyon was born. Today the company has grown into a very successful bicycle manufacturer and employs 350 people.
Shunning the traditional business model of having a regional distributor supplying a network of bike shops, Canyon have embraced the internet, and DHL’s fast delivery service, to sell direct to the consumer. Selling direct like this allows them to pass on the considerable savings to the customers, a fact that hasn’t gone unnoticed by a lot of UK cyclists in recent years.

This building we’re in is surprisingly small: I was expecting something vast. We’re told they’re starting to outgrow the building, which was purpose-built just a few years ago. Inside the four walls is the head office, where the designers and product managers are based, as well as a large customer support team to answer all email and phone queries from customers. With no shops to handle any problems, Canyon have to deal with all questions and concerns in this way, something they take very seriously.
That’s all upstairs. Downstairs is a slick shop open to the public with a full range of bikes, and a small selection of race bikes. There’s also a coffee bar. They do a mean espresso and the cake selection is fantastic.

As is the case with nearly all bike manufacturers, the frames are made in the Far East. Canyon, however, do all the assembly here, and build bikes up to order. The frames and parts arrive at one end of the building, and complete bikes emerge out of the other end, going straight onto a DHL lorry to be delivered around Europe.

When an order is placed, all the parts for the build, including the frame, fork, wheels, groupset and finishing kit, are placed on one of these trolleys. It’s then wheeled through to the first station in the process. To improve efficiency, they build the bikes in batches. Here’s a neat row of Ultimate CFX frames waiting to be built.

The parts destined for this particular bike build.

Around 250 bikes are built in two shifts every day, though this number varies depending on which bikes they’re building. Some, like the time trial bike, are more time intensive and take longer.

Due to the complexity of the TT bike, especially the handlebars and the cabling, one person builds the whole bike. All other bikes are passed from one station to the next, each dealing with a specific aspect of the build.

It’s a very tightly managed ship. Well, it is a German company, what else would you expect? This screen shows the staff their daily and weekly targets, and the red number is how far behind they are. It’s basically a digital whip!

A typical bike build can take about 45 minutes from start to completion. The CFX, however, takes about 2 hours to build, and passes through 16 stages. This series of stations that a bike passes through also allows Canyon to quality check the bikes constantly.

All wheels, like this rack of Mavic hoops, are checked for spoke tension. That’s hugely labour intensive but shows that Canyon are committed to delivering quality products.

Buy a Canyon bike, and this man has probably checked the spoke tension in your wheels.
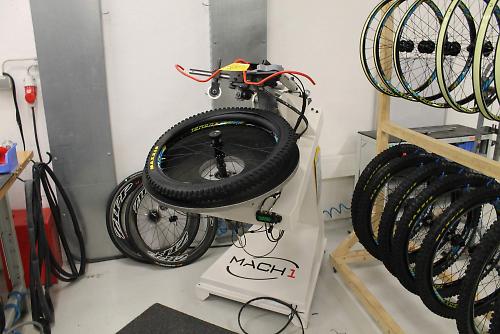
This machine speeds up tyre and tube removal and refitting.

Here's a CFX nearing the end of its journey.

And here's a bike boxed and ready to go. Kind of. The actual boxes don't have windows, they've just prepared this one to demonstrate how neatly the bikes are packaged in their custom-designed boxes. They have to ensure the bikes arrive in perfect condition.

That leads us nicely into the next department we’re toured through: the research and development laboratory. Canyon have a set of machines to test prototypes, and also to quality check production bikes. They’re clearly super keen on ensuring the product is the highest quality. Even if a product goes through a quality control in the factory in the Far East, they still like to do their own inhouse testing.

Some of the rigs are set to emulate EN tests, but Canyon make sure they test above and beyond those standards. They designed their own rigs in partnership with the local university. They continue to invest and have ordered four more testing rigs which are arriving soon.

A component will be put through up to 100,000 cycles. They leave it running overnight and over the weekends. They've got this remote controlled webcam so they can check in on it after hours.

This machine is testing head tube stiffness, measuring deflection.

This CT scanner is an impressive bit of kit. It’s also hugely expensive at €500,000, but Canyon justify it by noting that even one recall of a product would be significantly more expensive.

The CT Scanner allows them to inspect the internal structure of parts and frames. It’s mostly used to check production frames, but is also used in the development of new products. That's the inside of the seat tube on the screen there. You can see the joint between the two tube sections.

They check all their time trial bars and all forks, 150 of them a day. For frames they do random checks, about 5% of the production run, to ensure they meet their standards and there’s no defects in the carbon layup. The CT scanner allows them to check for any defective layup on the inside of the fame that would otherwise be impossible to see. They check all the team bikes as a matter of course.

Back in the shop, there's just enough time to have a look at a collection of race bikes. As you can see, this one belonged to Cadel Evans.

This one belonged to Luca Paolini.

And this one belongs to founder Roman Arnold. He's a tall chap, isn't he?
Thanks to Alex at Canyon UK for arranging the trip.
www.canyon.com
Add new comment
28 comments
Are there any other manufacturers producing bikes and selling directly to customers ?
So essentially they are the German version of Planet X?
manufacturer?????
should not that be an assembly warehouse?
my new Ultimate CF SLX arrived within 10 days from the day of ordering. Brilliant bike at an unbeatable price - the latest frame is such a step up from the previous CF SLX, much stiffer but still extremely comfortable on our typical British country lanes.
Quality product at a bargain price. I waited just over 3 months for my ultimate slx to be delivered with no communication from Canyon to inform me they're going to fail to deliver on the second or third due date. Oh well only ruined the one summer. Someone throw that "digital whip" in the skip, my bike arrived with a potentially dangerous loose front brake block which I found immediately , and a loose headset which went unnoticed for a few miles, the bearings on my nice new bike are now knackered, nice one Canyon. Still with the money I've saved I can get a decent bike shop to sort it out. You are cheap though Canyon, I'll give you that.
Never really liked their graphic design: how many logos do you need? We get it! You're called Canyon! It's all a bit desperate. And the ".com" is a bit "moneysupermarket.com" - it cheapens the whole look. Putting me off for now.
Just to give some balance on the delivery time, I ordered mine at the beginning of march and received it a week later. Maybe if you order in mid summer, which I deliberately avoided, they are deluged and the wait is much longer.
but on the downside UK Internet blogs do report customer delivery delays, however my cousin waited 8 weeks for Cannondale to deliver a basic Caad8 2013 model finally arriving June, Evans dealership at Aberdeen. Catch Canyon right they do offer excellent end of season discount
Canyon are a well kept secret. Five years ago I could have bought top or the range carbon, 10 speed Campag Record with (wait for it) Lightweight Wheels set (tubs) £3500 when the wheels were UK RRP £2200.... Just didn't have the money. Aluminium frames are a bargin as well as the carbon team frame set. Only problem was their daft frame cycle fit online system seemed confused, didn't match my expectations of frame size and fit but they have a UK office and a 30 days return policy I believe. If you can build and maintain your own bikes then Canyon is a serious consideration..
Still have Erik Zabel as a 'Hero' on their website and Canyon say they will not be getting rid of the doper and liar.
That kind of thinking turns me off them.
I read on Cyclingnews.com they had dropped him because of the EPO?
reminded me of a formula one type set up, very professional and recognizes that quality means sustainability, I can see them being very successful for many years to come.
Love my ultimate cf and unbeatable value. If you want your bike now got a bike shop.
Or just ride what you have and be patient it is worth it
I was happy to wait - about 8 weeks when I placed the order. However, the repeated delays from the initial date generally advised during the week when despatch had been indicated after significant chasing on my part got too much. And our Scottish summer is over. I can now wait until next year.
Unfortunately still waiting for my CF SLX ULTIMATE. Eight weeks delayed now
My SLX ULTIMATE was 2 months late but its worth wait. Which other bike company can supply 13lbs bike with campag Record and Mavic Exalith wheels for £3,500. My advice is just keep giving them grief at Canyon. I end up with a discount and some nice freebies.
I ordered a frameset and it arives two days later. Perfect ride 2 years later. Their prices are unbeatable for OTP and their outlet is beyond that.
I love the look of the TT bike but I don't reckon I could ride one. Or persuade the Mrs. that I need one.
All very nice, but putting Romanian wheels onto Far-Eastern frames in Germany isn't really German manufacture.
But the facility is nice though isn't it!? It has that German clinical feel to it like Audi's and the like. From what I know Rose have a similar business model too.
I don't think we should beat ourselves up to much about these sorts of things. We have other things going on here. Though it is a shame we appear to have let the corporations destroy our high streets.
German Efficiency? I have to laugh.
12 week delay from original order quoted delivery and not able to provide a definite date at that time. Ordered cancelled as 2014 model is likely to be available prior to recieving the 2013 one. I would strongly recommend ordering stock items only.
Delays were frustrating but compounded by an inability to communicate in a timely and clear manner.
You dont see companies creating brilliant stuff like this in the UK,professional productive profitable businesses that actually MAKE stuff
its all service industry,supermarkets and banking whores
This country really is an utter shithole
See, this is why you never get invited to parties.
They're not MAKING anything - they're assembling parts that are made in the far east. Plenty of firms in the UK are doing exactly the same thing. For sure Germany has maintained an impressive manufacturing base - this isn't it though.
Unfortunately still waiting for my CF SLX ULTIMATE. Eight weeks delayed now !
but when will they release their 2014 range?!?!?!
end of the month mate, to coincide with euro bike... i asked canyon the other day
Eurobike, at the end of August
Brilliant, just what I'd expect from a German company.
Reminds me of the neatness from the McClaren factory in the UK.
The TT bike is awesome, love the flat headed top tube!
Canyon%20visit%20(14).jpg