The German bike makers at Canyon have bought themselves a CT scanner specifically designed for testing frames and components and they reckon the benefits are already coming in.
CT scanner? 'CT' stands for Computed Tomography which is a highly developed form of X-ray where quite literally thousands of simultaneous cross-sections of a given subject are assembled by computer to form three dimensional images. Viewers of 'House' on TV will be familiar with anxious hospital patients disappearing into a large machine to have their internal organs checked out but, according to Canyon, the technology is already widely used in industrial processes but not, until now, the world of bicycles.
Canyon's founder and CEO Roman Arnold says, "This brand new acquisition represents a new benchmark in the cycle industry and is at the same time a further expansion of our pioneering role in that industry."

Over to the Canyon boss for this bit:
"The use of CT scanning equipment gives the testing of alloy and carbon frames and components an entirely new dimension. The system generates around 1000 individual images to create an exact 3-D computer animation of the frame or component, thereby allowing a highly precise and detailed examination of the material’s structure and of possible manufacturing defects. The 3-D images which are generated provide our R&D department with a significant increase in knowledge and take us a major step forward in the areas of quality control and customer service."
Mind you, if you were expecting a CT scanner that looks like the familiar medical machine with a lying-down human size tunnel, you'll be able to see from Canyon's own pictures that the bicycle factory version looks more like an industrial spray booth but then it needs to if awkward-shaped objects like bicycle frames and wheels are going to be subjected to the all-seeing eye of the system.
According to Canyon, the CT device has now been installed at the Koblenz headquarters for a few weeks and has already completed several successful test runs. "Alongside the specific testing of visibly faulty components and frames from now on carbon components and frames in particular will undergo random quality control tests upon entering our warehouse."
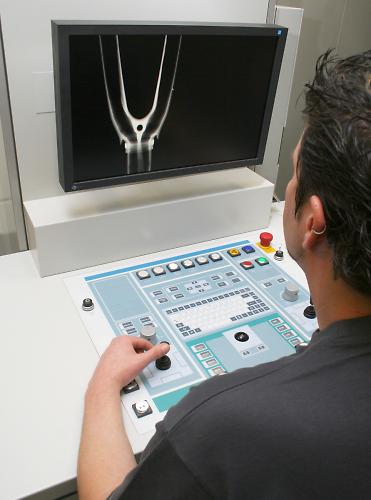
Needless to say, though, what the engineers are really excited about is the potential for developing future products. "This will allow us, for example, to analyse the possibility of consistently improving and reducing the weight of our products whilst at the same time increasing their level of safety."
Add new comment
6 comments
uhhhhhh, how is this different from a 3D scanner? All its doing is give them a CAD model to play with: without integrating their 'CT' model with an aerodynamics toolkit its useless.
Unless you are looking for cracks in the bike, but that doesn't make faster bikes, just less mistakes!
I imagine that it will allow them to produce prototype frames, wheels etc, subject them to testing and then see if there is are any internal changes to the composition of the materials. Hence, they produce components that are as light as possible, with extra strength in areas that they have seen to be weak.
It is not always possible to see internal fracturing/damage to composite components without the use of x-ray, but a single x-ray only shows one part of the component from one angle, this will allow them to see the whole product from all angles, speeding up the R&D process.
You're right, this is just quality control. Though an internally de-lammed bike would be a bit slower...
What I imagine it does do though, is allow Canyon to not have to work 'on the safe side'. They can design things to the limit of the material, because they know they can check it properly, rather than beefing bits up where they can't be sure.
damn, beaten to it....
It's Computed Tomography rather than Computer Tomography.
I've been reading way too many PACS specifications this week hence the pedantic correction
Ha! Thank you - amended...
"Useless?" I don't think so. roadracedave and localsurfer both makeexcellent points. And anyway what's wrong with making products reliable as well as fast, light and aerodynamic. The aero frame that crumples due to being fettled for lighter weight in the wrong places won't finish the race so is bugger-all use to anyone. As Mr Brailsford says in another context: it's all about the marginal gains once you're at the edge of experience.