The ultimate guide to frame materials: what's best for bikes?
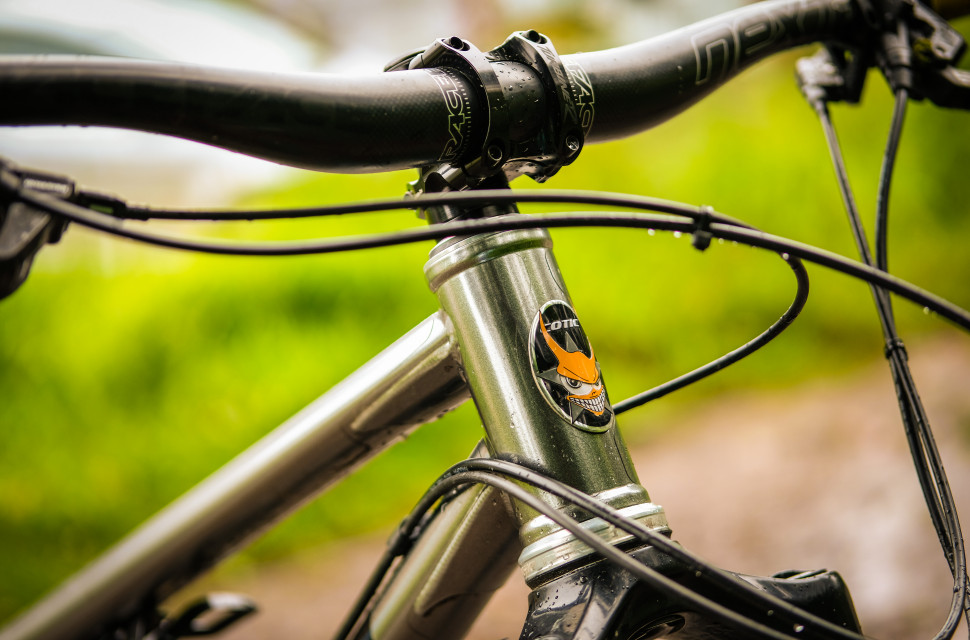
There's a lot of myths, marketing hype and dubious 'engineering' talk surrounding frame materials. with different camps exalting (or denouncing) the fabled smooth ride characteristics of steel and titanium, the harshness of aluminium and the stiffness of carbon fibre.
- Best mountain bikes you can buy for under £2,000
- The best hardtail and full suspension mountain bikes you can buy for under £1500
- Best MTB's that you can get shipped straight to your door
[Updated 21st June 2020]
In reality, while each material has its advantages and disadvantages and ride quality is largely determined by good frame design that works with and understands the properties of the material used.
Understanding material properties
All metals used for bikes are an alloy. We don’t use pure iron (steel is a mixture of iron and carbon), pure aluminium or pure titanium. Instead, additional elements are added to improve the basic properties of the metal. Carbon fibre is slightly different, but we will discuss this later.
Cycling companies will often talk about using aerospace grade metals – but the reality is that designated alloys have to conform to certain quality requirements regardless of whether they are used in an aircraft or a bike frame. There's likely to be no difference between a bike that claims to be made from 'military grade' material and one that isn't
The main property of importance for bike frame design is Young’s Modulus. This describes the material’s stiffness – the tendency for it to return to its original shape under load. Young’s Modulus is similar for metals made from the same alloy.
Contrary to what you might expect, outright strength is less important. By designing a frame to be stiff enough, it will also usually be strong enough to withstand cycling loads. However material toughness is essential in ensuring damage resistance. A tougher material is able to absorb more energy before failing, meaning it will bend rather than breaking in a brittle way.
Repeated loading of materials can lead to fatigue failure. Steel and titanium have a fatigue limit, a maximum stress below which the material can be loaded an unlimited number of times without failing.
off.road.cc on WhatsApp
All the latest offroad cycling news, tech and buying advice straight to your phone.Follow our WhatsApp channel here
However, aluminium has no limit and given enough loading cycles, will fail under very small stresses. That doesn't mean you should listen to people who claim aluminium frames are much more prone to failing in the real world however; by designing frames to minimise the maximum stress levels experienced, the lifetime of the frame will be more than long enough to cover a normal lifetime of use.
Form and function
Control the geometries and dimensions of the tubing used to build the frame also has a very large influence on ride characteristics. As tubing diameter increases, so does its stiffness. For a given amount of material (and weight), we can increase the diameter of a frame tube but must simultaneously reduce its thickness. Doing this, doubling the diameter results in four times the stiffness.
To maintain the same stiffness for a lighter weight, we could use less material in a larger diameter, thinner walled tube. However, there is a limit to how thin tubing walls can be made before they become susceptible to damage, denting and more importantly buckling.
Bicycle frame design is about selecting tubing dimensions to appropriately tailor the stiffness and compliance to the desired ride characteristics. The elastic modulus, coupled with tubing dimensions is what will influence the stiffness of a frame. In theory, it would be possible to build identically handling bikes in any material, matching relative material stiffness through appropriate tubing choice.
Steel
Steel is the mother of all engineering materials. It is incredibly strong, very stiff, easy to work with and cheap to manufacture.
This workability is part of the reason steel has had a resurgence with smaller builders. However steel is “density challenged” – frames are usually heavier than their aluminium or titanium equivalents.
Steel will rust if neglected – though frames can be treated and manufacturers such as Reynolds produce stainless tubing that largely negates this problem.
Most cycling steel alloys are based on 4130 Chromoly. Heat treating can improve material properties – that's heating and cooling the material in a specific way. Reynolds 525 and 725 use the same base alloy (very similar, if not the same as 4130), but 725 has improved properties due to heat treatment. Different steel alloys, such as niobium, mangaloy and of course stainless, are also used.
In the past material and production limitations restricted the minimum wall thickness achievable with steel. With the introduction of ultra-high strength (UHS) steels it has been possible to reduce wall thicknesses, down to 0.38mm with Columbus Spirit tubing.
In theory, with thin enough tubing, it would be possible to build a frame with weight on-par with the lightest frames today. However durability would suffer significantly, with such thin walled tubing being highly susceptible to denting, damage and buckling.
Assembling thin walled tubing also becomes difficult to assemble, with heat from welding affecting heat-treatments and reducing strength in the weld area. Some steels, such as 853 by Reynolds actually increase in strength after cooling due to the way they have been treated.
Butted tubing, tubing with variations in the wall thickness along its length makes welding easier whilst maintaining thin walls. For example a double butted modern steel tube may be 0.7mm at either end but 0.4mm along most of the length of the tube.
In the event of a crash or damage there is a significant threshold in which steel can deform before failing. In other words there should usually be significant warning and visible bending before a steel frame will fail completely.
The ability to repair steel can often be overlooked. It is usually possible to bend frames back into alignment and repair damage. I for one, was glad to be able to reattach rack mounts during a bikepacking expedition - not something that is as easy with other materials.
Aluminium
Aluminium alloy is nowhere near as strong or stiff as steel, but has around one-third of the density. Early frames were described as “noodly” because they used similar tubing dimensions to the more traditional steel – the change in material stiffness hadn’t been taken account of and they flexed significantly.
This is why we now see aluminium bikes with the oversized tubes that are needed to give the required stiffness to the frame.
An aluminium frame will use more than twice the volume of material as steel. Wall thicknesses are around twice that of steel and tubing diameters are around 20-30% larger to maintain suitable stiffness. However, the lower density will result in a frame weighing around 30% less than a steel frame.
There are two main aluminium alloys in use in the bike industry today – 6061 and 7005. There will be a further designation indicating the tempering process – often T6 – the alloy has gone through. Whilst explaining this is outside the scope of this article, this is a heat treatment that improves the properties of the alloy.
In practical use the different alloys will be indistinguishable, though 7005 is slightly cheaper to work with as it requires less overall processing. There are some more exotic alloys, including scandium and lithium, in limited use, which aim to reduce frame weight even further.
Aluminium has a reputation of having a harsh ride. This may have been true with early frames but is not the case anymore. Frames tended to be overbuilt in weld areas to avoid cracking due to fatigue. Welds can act as stress concentrators and nowadays, many high-end alloy frames, such as the Cannondale CAAD series, smooth out the weld area to avoid any localised stress concentration.
The excessive use of more material to reinforce frames resulted in stiff frames before designs became more refined. However, nowadays the ride of an aluminium frame can be exceptional. Nonetheless, aluminium is a more brittle and weaker material than steel, and as such frames tend to be slightly overbuilt to make frames stronger and give a larger safety margin.
Frames are designed so that stresses are low enough that in normal loading it will not reach its fatigue life within its usage lifetime. Adding material in highly stressed areas can also help redistribute stress to minimise the stresses experienced.
Hydroforming is used with aluminium tubing to form complex shapes. As 6061 is more ductile, it is more likely to be formed this way. A tube “blank” is put inside a die. Fluid is run through at incredibly high pressure forming the tube to the shape of the mould it is in. This allows the dimensions and geometry of the tubing to be tailored to provide certain ride characteristics and can also help redistribute stresses in the frame.
Steel can also be shaped, though hydroforming for steel is not really applied to bicycle tubing. Instead tubes are modified mechanically. Ovalised tubes essentially act as a larger tube in one direction, and as a smaller tube at 90 degrees to this. This provides stiffness in one direction but compliance in the other.
Titanium
Titanium has its provenance in the aerospace industry, where it is widely used. 3Al-2.5V is the most widely used alloy, though the higher performing 6Al-4V also exists.
While as an element titanium is very abundant, it takes a lot of effort to refine and process into the tubing used for frames. It is relatively hard to work with, wearing out tooling more quickly and requiring a controlled atmosphere for welding. All of this drives up its cost significantly.
However titanium genuinely provides a frame for life. It is incredibly hard-wearing and corrosion resistant, which is also why it is often left unpainted. It can be made to have very high strengths.
Less dense than steel but heavier than aluminium, it also falls roughly in the middle in terms of stiffness. It is more difficult to find butted titanium tubing, though as its popularity increases manufacturers provide more and more options.
Carbon fibre
Carbon fibre, or more properly Carbon Fibre Reinforced Polymer (CFRP), is the new kid on the block. It is completely different because it can be “designed” specifically for its application. CFRP has incredible strength and stiffness for its weight, allowing very lightweight frames to be built.
Metals are isotropic, meaning their mechanical properties are the same in all directions. In metal frames a by-product of building the frame to the required strength is that the tubing will also resist “non-cycling” loads. It resists loads in all directions.
On the other hand CFRPs are anisotropic. Their properties are dependent on the direction of load. Strong in the loading/design direction, frames may be quite flexible in another. Indeed on some frames it is possible to visibly squeeze the tube walls together.
CFRP consists of microscopic carbon fibres aligned and held in a resin matrix. The fibres have diameters down to 5 micrometres, much thinner than a human hair. These are bundled together to form a tow.
The fibres are like ropes, providing most of the strength. They can withstand tension, but would crumple if compressed. The resin matrix ensures the correct alignment of the fibres, and provides additional compressive strength. The resin must be cured to set the shape of the composite.
Most manufacturers now use pre-preg carbon; sheet of carbon fibres that are pre-impregnated with resin. These are usually uni-directional - the fibres are all aligned in one direction - giving high strength along the axis of the fibres.
The sheets must be built up in multiple layers - forming a laminate - placed at different angles to withstand different loading directions. The way this is done is know as the layup. Woven pre-preg may be used as an impact resistant top layer and to give a better surface finish.
Pre-preg sheets are used to produce monocoque frames. The sheets are cut to shape and layered around a core. A frame may use hundreds of individual pieces. This is then placed inside a mould and cured at high temperature and pressure. The core is commonly a removable inflatable bladder which applies internal pressure during the cure.
The quality of the layup is very important, with poor bonding between layers in the laminate causing significant weakness. The pressure during curing aims to remove any voids and creates a cohesive, strong laminate. Manufacture quality control is essential.
The key advantage of carbon fibre is that layups can be tailored to achieve specific ride properties. CFRPs allows reinforcement of the frame by adding more material in specific areas. An obvious example is the beefed up bottom brackets designed to resist flexing during pedalling. Fibre orientation can be modified to favour stiffness or compliance for more race or comfort focussed frames.
Often carbon fibre with different properties will be used in different areas of the frame to tune compliance and stiffness as required. High modulus carbon can be used to stiffen key area. Different fibre types can also be used to further tune the composite properties. For example Kevlar and Vectran are used to provide additional crash resistance.
The alternative to using pre-preg is Resin Transfer Moulding (RTM). This involves weaving “dry” carbon fibre around a mandrel – a removable core. This is then impregnated with resin under a vacuum and cured. The individual tubes must then be bonded together.
Look are one of the few manufacturers who use this method, and implement advanced techniques to form complex tube shapes and the complete frame. RTM arguably gives even better control over localised material properties, and can lead to overall higher quality carbon fibre parts.
However the largest limitation of carbon fibre is that it is an inherently brittle material. Whilst a metal will bend before failing completely, when carbon reaches its strength limit, it will fail suddenly. Failure is very unlikely but when it does happen is likely to be catastrophic.
The design of frames must be carefully considered to withstand real-world scenarios and loading. That said, a crash that destroys a carbon frame is likely to destroy most other frames as well.
It is potentially more difficult to identify damage with a carbon frame – where a metal frame will have bent, a carbon frame may have cracks that may not be visible. Thorough damage assessment on carbon frames is significantly more complicated.
While it is possible to repair carbon fibre, it could be difficult to do satisfactorily without knowing the (proprietary) details of the layup of the frame to be repaired. However many manufacturers do offer crash replacement programmes.
There is significant interest to improve the impact resistance of carbon fibre by modifying the resin and fibres as well as using novel layups and resins. It should be clear that there is significant expense in developing a high end carbon frame, and the cost is not just associated with manufacture, but also the detailed engineering of a “designed” material.
Good vibrations
One of the unique abilities of carbon fibre is its ability to damp vibration. This is due to the resin, which effectively filters out high frequency vibration – i.e. road buzz. What some people describe as dead feeling, others exult as hugely comfortable.
Modifying the resin properties can also be used to improve these properties. By “rubberising” the resin, it can absorb more vibration. Bianchi Countervail technology incorporates a vibration dampening layer in the layup that performs a similar function.
In contrast metals act like springs and have no significant damping. However frames can be designed to be compliant, i.e. deflect under load providing additional comfort. Tuning compliance by selecting appropriate tubing dimensions and geometries is the key way to control comfort in metal frames.
Carbon frame ride can be controlled in much more detail by varying the layup in different areas of the frame to tailor for compliance or stiffness. Discussing the intricacies of this is something that could take up a whole additional article.
It should be noted that the ability to soak up “road-buzz” is not really related to the ability to absorb larger shocks or impacts. This has much more to do with frame geometry affecting how forces are transferred to the rider. Comfort and frame design are perhaps something we will leave for another day.
So which is best?
It is possible to make an excellent frame with any of the materials mentioned, but for a high performance frame, the choice will usually come down to be either carbon fibre or aluminium. There is little doubt that a carbon frame can be made the lightest, so it wins, assuming you just go by the numbers. Aluminium provides an excellent compromise, allowing lightweight bikes to be built at more reasonable costs. Unfortunately it is the case that you get what you pay for, and a carbon frame will be more expensive than a metal equivalent.
However, many, there is something romantic about a nicely made, high end steel frame. With titanium and steel we move towards more of a niche market. Production frames are of course available, but these materials are also the purview of custom builders who will design a bike fitted to you.
At the end of the day you have to choose where your priorities lie. Do you need the marginal gains that a lightweight carbon frame can provide, do you want the lightweight but cheaper compromise of aluminium, do you want the prestige and life-long durability of titanium, or do you want the traditional and versatile steel?